The flowmeter is widely used in many flow measurement aspects. This article mainly introduces a microwave solid flowmeter and its application in flow measurement.
1 Introduction
The large coal-fired units of thermal power plants generally use a direct-blowing pulverizing system. Each coal mill outlet has 4 to 8 primary air pulverized coal pipes directly connected to the boiler burner, and the pulverized coal is transported to the boiler through the powder conveying pipeline The burner burns. Due to the different lengths of the pulverized coal pipes and the number of elbows, the pressure loss of each pipe is different, resulting in uneven distribution of pulverized coal between the pulverized coal pipes, resulting in the burner not being able to operate under the optimal air-to-coal ratio Normal operation reduces the combustion efficiency, increases NOX emissions and increases the boiler failure rate.
2. Analysis of problems in pulverized coal testing
When the distribution of pulverized coal among the pulverized coal pipelines is uneven, the concentration of pulverized coal will be too high or too low, and the flow rate will be too high or too low.
When the concentration of pulverized coal is too high, the following conditions will occur:
The pulverized coal is blocked, and the pulverized coal cannot be transported into the furnace. At the same time, the pulverized coal in the pipeline spontaneously burns and the powder pipe is burned; the pulverized coal is not completely burned, the efficiency is low, the CO increases, and the heating surface in the furnace and the heating surface of the superheater are exacerbated High temperature corrosion; local slagging in the furnace and superheater seriously affects the normal operation of the boiler.
When the concentration of pulverized coal is too low, the following conditions occur:
Furnace temperature is reduced, easy to flameout, boiler air pressure is reduced, can not meet the load requirements; produce a large amount of NOX, pollute the environment, high temperature of the superheater, and even cause the superheater to burst the tube and other accidents; in order to increase the air pressure, increase the primary air (powder conveying pipe) flow rate The tangential circle of the hearth is offset from the center of the hearth, causing partial slagging in the furnace wall, excessive temperature deviation of the smoke on the heating surface of the tail, and even causing tube explosion.
When the flow rate of the mixture of pulverized coal and air is too fast, it will affect the optimal concentration of pulverized coal, and the following conditions occur:
Aggravates the wear of the powder conveying pipe; the flow rate of the burner outlet mixture is too fast, and the combustion lags, causing the center of the flame to deflect and easily cause local coking of the furnace wall and local overtemperature explosion of the superheater at the end of the furnace; incomplete combustion, carbon content in ash And the exhaust gas temperature increases, reducing boiler efficiency.
When the flow rate of the mixture is too slow, in addition to affecting the optimal pulverized coal concentration, the following conditions occur:
Pulverized coal deposited in the powder conveying pipe increases, causing pipe blockage; causing spontaneous combustion of pulverized coal, or even explosion of pulverized coal pipeline; the flow rate of the burner outlet mixture is too slow, and a large amount of pulverized coal is separated from the main airflow. Removal over a long time causes increased coal consumption, and It causes flameout of the furnace and secondary combustion to block the ash outlet in the lower part of the boiler.
3. Pulverized coal measurement solution
The method to solve the above problem is to measure the flow rate and mass flow rate of pulverized coal in the pulverized coal pipe online, and use this as a reference to adjust the secondary air volume of each burner to meet the best condition of combustion.
In the direct-blown pulverizing system, the control of the amount of pulverized coal is monitored by the amount of primary air entering the boiler pulverizer. Therefore, the primary air flow signal is particularly important. For the flow rate measured by the Venturi tube flowmeter, when the current flow field is stable and uniform, the flow coefficient K is a constant, and only the fluid density and pressure difference values ​​need to be measured to obtain the ventilation volume. Due to the constraints of working conditions and equipment conditions, the differential pressure signal is distorted, the coefficient K is not constant, and the maximum deviation is more than 34%. Therefore, it is unreliable to control the amount of coal entering the boiler by adjusting the air volume through the baffle. When the boiler load increases or decreases, the furnace technician can only adjust the wind coal based on the field experience and the reference air volume detected. If an online measuring instrument for pulverized coal flow and concentration is installed in the powder conveying pipe (ie primary air pipe), the amount of pulverized coal can be optimally controlled, the coal consumption can be reduced, and the labor intensity of the furnace worker can be reduced, and the working environment can be improved. For the direct-blowing pulverizing system, installing the on-line measuring device for pulverized coal flow and speed on the primary air pipe, in addition to solving the above-mentioned two-inlet and two-outlet coal mill air volume measurement errors and unreliable problems, can also find direct The air lock of the blow-off separator leaks, does not work and other malfunctions.
4. Microwave solid flowmeter measurement system
4.1 Measuring principle
The microwave solid flowmeter adopts the leading microwave ultrashort pulse technology and is developed for the detection of the material flow in various solid conveying metal tube grooves. The microwave solid flowmeter MF3000 uses the microwave energy field and the refraction of the solid particles to the microwave and the Doppler principle. The sensor emits a low-energy microwave signal to the solid material in the conveying metal pipe / slot. The signal is reflected by the material and then received by the sensor . The density of the material is measured by the microwave reflection energy of the moving material, which is equivalent to a microwave counter to determine the flow rate of the solid material. It is suitable for the diameter of solid particles (powder) from 1nm to 1cm, and the measurement accuracy is 1-3% (after calibration).
4.2 System composition
A complete set of microwave solid measurement system includes: sensor probe and mounting base; communication unit (optional); transmitter (connecting sensor probe and communication unit). The RS2485 Modbus connection is used between the sensor probe and the communication unit. When the distance exceeds 1.8m, a transmitter is required. The system composition is shown in the figure.
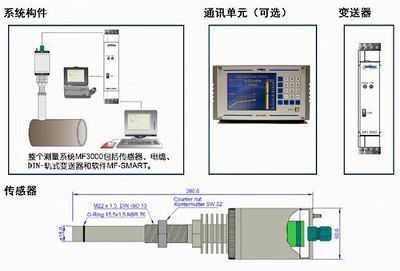
4.3 Installation of microwave solid flowmeter
According to the situation of the upstream and downstream areas of the coal pipeline, select the appropriate installation point. When the pipe diameter is greater than <200mm, 2 to 3 sensor probes should be installed on each coal pipe. The gap between the sensor probes is 150mm, and the angle is 90 ° or 120 °. For applications where the material falls freely (such as after a screw feeder or a rotary valve), the best installation position is 300 mm after the material falls. When installing, first weld the sensor probe base to a fixed point, then drill a <20mm hole from the sensor probe base into the pipe, insert the sensor probe and install the nut to make the sensor probe measurement surface flush with the inner surface of the pipe or lock Back to 1 ~ 2mm.
4.4 Calibration of microwave solid flowmeter
The calibration method of the microwave solid flowmeter must be calibrated online by the actual measured medium. For the calibration of pulverized coal mass flow in thermal power plants, it can be calibrated by the special coal powder sampling system of Danish M & W.
4.5 Improvement of control after the application of microwave solid flowmeter
The boiler pulverized coal flow measurement and the first and second (three) secondary air measurement systems are used as separate DCS systems, real-time online monitoring of the wind speed, nozzle speed and air volume of the first and second (three) secondary air ducts, and each primary air duct Parameters such as the concentration of pulverized coal and the amount of pulverized coal to guide the operating personnel to optimize and adjust the boiler combustion.
The pulverized coal flow measurement signal is sent to the DCS, and then the corresponding pulverized coal quantity is balanced according to the coal type. It is usually simple and economical to measure only the unevenness of the pulverized coal quantity in the system, and calculate the required value of each burner according to the measurement result. Because the air volume adjustment is relatively easy to achieve, as long as the damper flap can be used to control the secondary air volume of the burner. Although the imbalance in the amount of pulverized coal between the burners has not improved, it can ensure that each burner operates within the range of the design air to pulverized coal ratio.
According to the measurement results, the furnace worker adjusts the proportion of air coal in the primary air pipe (that is, the powder conveying pipe) to the best state and matches and balances each other, thereby changing the original habitual operation method of adjusting the air door baffle and the amount of powder according to experience.
For the direct-blowing powder-feeding boiler, the coal feeder speed can be adjusted by the cumulative value of the pulverized coal flow of each pulverized coal pipe of the coal pulverizer to achieve accurate adjustment of the coal pulverizer output.
Aiming at the problem that the heat signal detection delay in the boiler combustion regulation system is large, which causes the regulation of the combustion regulation system to be insensitive and restrict its load response speed and regulation quality, a closed loop regulation link is added to the heat regulation control link to overcome the powder In order to improve the sensitivity of the combustion regulation system.
The closed-loop control of the amount of powder delivered by each primary air pipe of the boiler can truly achieve automatic optimization of the boiler combustion conditions.
5. Conclusion
By improving the accurate detection of pulverized coal flow (concentration) and air volume (speed) of coal-fired units, the balance of pulverized coal concentration and air volume (speed) of each coal pipe can be met, so that the combustion flame of the boiler is kept at the center of the furnace to ensure a balanced combustion output. The purpose of optimizing combustion and prolonging the service life of the boiler and maintaining the safe and economic operation of the boiler for a long time can reduce the coal consumption of the power plant by 3% and reduce the NOx emissions of the thermal power plant.
Shallow basin allows easy access for all bird types
Fill a bath with fresh, shallow water and enjoy watching all the birds congregate from the comfort of your couch or while at the table having dinner with your family or working on art projects with the kids.
Elegant and weather-resistant
This elegant birdbath is perfect for pairing with a Bird Feeder to coax a variety of birds outside your window during any season. With Alpine`s birdbaths, your yard will be the delight of humans and winged creatures alike!
EASY TO ASSEMBLE - Constructed with simple components that make it easy to assemble; The bowl is easy to attach by screwing it onto the base, while the base is hollow and convenient to fill with materials
Antique Flower Birdbath, Garden Bird Bath, Glass Bird Baths, Bird Bath Bowl, etc
HISMOK(SHENZHEN)TECHNOLOGY CO.,LTD , https://www.will-trade.com