Silk production is a subsystem of the cigarette production process. It is a production line that processes pre-processed tobacco sheets and stems into raw tobacco products that meet the requirements of cigarettes. The entire production line is a collection of light, machinery, electricity, and information. Integrated system engineering. It is composed of many parts, each part has a lot of control points and collection points. As far as the whole system is concerned, there is a large amount of data information exchange between each part. The key to control is to realize the automation of process, production and management. This paper introduces the control method of cigarette thread based on industrial Ethernet.
introduction
Silk production is a subsystem of the cigarette production process. It is a production line that processes pre-processed tobacco sheets and stems into raw tobacco products that meet the requirements of cigarettes. The entire production line is a collection of light, machinery, electricity, and information. Integrated system engineering. It is composed of many parts, each part has a lot of control points and collection points. As far as the whole system is concerned, there is a large amount of data information exchange between each part. The key to control is to realize the automation of process, production and management. In order to protect the previous investment and realize the seamless connection of control, it is necessary to adopt a control scheme with high reliability, good stability, strong anti-interference ability, fast communication rate, system security, compliance with environmental protection requirements, low price, and low maintenance cost. Sensors, PLCs, computer graphics, networks, communications, and many other rapidly-developing technologies are combined together, and are designed with a combination of convenient and flexible hardware and software modules to meet the various process control and management requirements of users.
ã€Control system configuration】
Choice of control system
In order to make production quickly reflect the latest market demand and shorten the time to market of new products, this requires continuous information flow within the scope of the tobacco factory for strategic decision-making:
From the first production line, to the factory control level, to the management level. Therefore, information technology, especially information technology based on production automation will become the main force to promote production efficiency, reduce production costs and enterprise innovation. As a strategic technological innovation, profinet provides a complete network solution for the field of automation and communication, including the latest technologies in the current field of automation such as real-time Ethernet, motion control, distributed automation, fail-safe and network security. And, as a cross-vendor technology, it can be fully compatible with industrial Ethernet and existing fieldbus (such as Profibus) technology to protect existing investments.
It is composed of industrial Ethernet switches with network management functions and three-layer switching routing functions. The redundant fiber ring network is used as a workshop-level backbone communication network. It is mainly used for network communication between control systems and between control systems and centralized monitoring systems. communication.
According to the division of the process section and the control range of each control system, an industrial Ethernet switch is used to construct a star control sub-network for each process section control system to provide network communication between the main control device of each control section and the io site. Each control subnet can be connected to the backbone network through a switch.
Construct a sub-network for the centralized monitoring system. On the one hand, the network is connected to the workshop backbone network through an Ethernet switch to complete the network communication between the centralized monitoring system and the control system; on the other hand, it is connected to the plant-level network through the switch or web server. Class-level data communication provides a network interface. At the same time, a hardware firewall is installed at the interface with the plant-level network to protect the security of the centralized control system and the control system and to prevent infringement from the plant-level network and the internet.
All network equipment adopts dual power supply to ensure that the network equipment has redundant power supply and ensure the stability and reliability of the network.
Selection of configuration software of host computer
System requirements for scada (data acquisition and monitoring system): through industrial Ethernet profinet, with the ability to communicate with multiple lower computer systems, real-time monitoring of the working status of multiple lower computers, showing the working curve in the production process; Remote control capability; collect data to the lower computer, store, query, display and print historical data. Therefore, in an automatic monitoring system, the running monitoring configuration software is the system's data collection and processing center, remote monitoring center, and data forwarding center, which together with various control and testing equipment (such as plc, smart instruments, etc.) can quickly form Responsive control center. This system selects wincc (windowscontrolcenter) 6.0 configuration software of Siemens company. wincc has powerful functions to control the automation process, is based on personal computers, and has a highly cost-effective scada-level operation monitoring system. Install the server version and redundant software packages on the two servers, and install the running version on the workstations.
Selection of other control system components
Under normal circumstances, PLC, on-site i / o and other devices can only use products that comply with iec standards. However, due to the use of the latest industrial Ethernet profinet, the interface of related devices has new requirements. plc requires a profinet interface, and the coupler of the field i / o substation requires a profinet interface. In addition, the switch requires support for the profinet function so that real-time signals can be transmitted. Among them, plc main station uses s7-300 / 400plc; remote i / o uses et200s that supports profinet technology.
The control layer backbone network is constructed by the latest Scalancex series switches to flexibly build electrical or optical industrial Ethernet; the network topology, type, and number of ports can be easily adapted to the factory layout. It has a high degree of network availability; even in the event of failure, it can be reconfigured through a very fast network (<0.3s), reliable communication; through sc interface (Gigabit Ethernet), st interface (Fast Ethernet) and pre-assembly Optical fiber, which can realize simple optical fiber connection technology; network configuration can be easily carried out without calculation of transmission time; application of signal contact, digital input, snmp, e-mail and profineio diagnostic functions, monitoring and diagnosis are very simple; Through the integration of the sfm in the simatic system fault message concept, the sps / HMI engineering cost is reduced.
Scalancex200 is connected to the profinet network, and the backbone network uses scalancex414-3e to form a ring-shaped optical fiber redundant network to ensure normal communication when a point of failure occurs on the network. You can also expand the network at any time without interrupting communication to fully ensure the reliability of the system. The scalancex400 switch provides a gigabit communication interface for the upper management network, and also provides an open platform for the integration of various subsystems. This type of switch fully supports vlan and routing functions, effectively reducing network load and preventing network storms. Further improve the reliability of the network. Scalances module connecting the control network and the external network of the plant can isolate the non-secure connection between the internal network and the external network. Effectively shield the unauthorized access to the external network and the spread of other unsafe information, while at the same time ensuring the communication of effective information. As all the sub-systems, such as: silk making line, dust removal line, formula library, co2 expansion line, public power system, energy management system, etc., use profinet network, unify the interface of all field devices, and realize the integration of multiple networks. The unified profinet system interface makes the entire workshop in a centralized monitoring state, enhances the transparency of the entire system, and effective data collection and transmission are more convenient and fast. All these provide great convenience for device management. At the same time, the concept of cba was introduced into the programming, and each sub-system was used as its own independent component, and they were connected into a unified system through imap software. It greatly simplifies and facilitates the complexity of communication programming and debugging, saving a lot of time. The use of a large number of industrial-grade optical fibers and industrial-grade connection accessories also makes every small connection in the network unbreakable.
vlan division
Figure 1 shows the division of vlan. If the virtual LAN technology is not set for the switch, the LAN switch can only exchange the individual information of the group that determines the destination address. Before sending data packets, each site must broadcast the MAC address of the destination to be queried. At the same time, because a large number of application layer software needs to broadcast certain data packets, and these data broadcast packets only need to be sent to a certain group of users, if there is no vlan, these packets will quickly occupy a large amount of resources in the entire network, and still act like a hub to forward broadcast information to all ports of the switch. This prevents normal data packets from grabbing normal bandwidth and seriously affects network efficiency and performance.
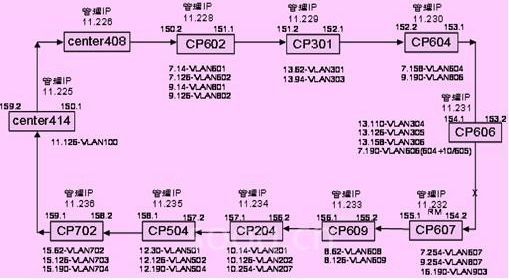
[Realization of control system and its difficulties]
The profinet switch builds a redundant fiber ring network. The electrical equipment of each process section is no longer physically divided, and all are connected to the industrial Ethernet profinet nearby. The logical structure of each technology section is completed during configuration, regardless of the hardware location.
The on-site operator terminal communicates with PLCs of all control sections through profinet to realize the authorized monitoring of the equipment in the relevant control section. At the same time, it also connects with the production management layer through profinet and obtains the production operation plan, batch tasks, recipe parameters, etc. directly from the production management layer Production data, and pass the production information of the relevant production section to the production management. The data server is also connected to the industrial Ethernet profinet via Ethernet to collect relevant data. The wireless Ethernet switch can make the staff's wireless equipment easily connect to the network to carry out work. Fig. 2 is a structural diagram of a wire-making control system.
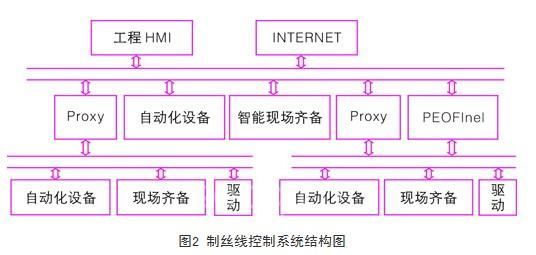
In the design of this solution, the most problematic place is communication, and the most troublesome place for on-site debugging is also communication. Therefore, for the part of communication, the frame structure of the system must be clearly understood (Figure 3 is the topological structure diagram of the silk thread) The devices that need to be communicated must be debugged before installation. Make sure that all the modules that need to be communicated can communicate. For example, console computer, touch screen, plc, inverter, other plc, some smart meters and instruments. Due to the large size of the system, due to the use of normative restrictions, the coordination of these modules should be considered when configuring the system hardware. When installing i / o modules, modules of the same model are usually placed together. However, due to the larger system, we use the output mode
If the block and the input module form a loop, the modules involved in the parameters of a loop are placed on a rack. When the base is installed (rack), after deciding the location of various control components and wiring ducts in the control box, the hole position should be calibrated strictly according to the dimensions shown in the drawings, and the fixing screws should be tightened until the base is firm after drilling. Before installing the power supply module, you must also pay attention to whether the grounding terminal of the power cord is connected to the metal chassis. If the grounding is not good, it will cause a series of problems, such as static electricity, surge, external interference, etc.
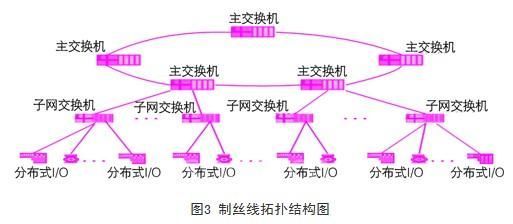
[Functions completed by the control system]
Batch task management
The computer receives the production batch tasks from the mes system, and decomposes the production batch tasks to the corresponding control section monitoring machine. The monitoring computer has 3 control selection modes, namely mes control / remote control / local control. During normal production, select the mes control mode, and the control system executes the batch task issued by the mes system after the management computer is decomposed; when the mes system fails, select the remote control mode, the control system executes the batch manually entered on the monitoring machine Task; when you need to debug and overhaul the equipment on site, select the local control mode, and you can perform local control of the motor through the on-site start and stop buttons.
Centralized monitoring function
The control computer monitors the production line in real time through a graphical interface. The control functions include the selection of the control mode of the production line, the setting of process parameters and equipment parameters, and the start and stop operations of the production line. The monitoring function adopts a graphical interface and is completely arranged according to the production line process flow. It has the function of displaying the running status of the production line equipment stand-alone, segmented or global process flow, and real-time display of process parameters and equipment parameters. The monitoring machine also has a security permission management setting function. Operators or system administrators must log in first to enter the monitoring system and perform permission control through the security level of different user identities, thereby ensuring the safe and normal operation of the system.
Production reports, statistical functions
After each batch of tasks is completed, a production report is automatically formed, including the task batch number, the recipe parameters used, the start and end time, and the statistical parameters such as the maximum, minimum, average, and standard deviation of important process indicators, which is convenient for the quality inspection department to evaluate the product quality. .
Device control function
The control system has two working modes, manual and automatic. When the equipment is repaired, a single manual mode is used; during normal production, the automatic mode is used.
Motor protection and emergency power off function
The control system provides a protection function for each motor, and provides an emergency power-off function at the same time. Set an obvious emergency button at the key position of each process section, so as to quickly cut off the power supply and control power of the entire process section in an emergency.
Loop control function
The pid loop control is needed for the temperature of the leaf cylinder, the pressure of the temperature increasing humidifier and the flow rate of flavoring. The pid parameter is set on the monitoring machine. There are two control modes: manual and automatic. In manual control mode, the output of each loop controller is directly adjusted by the operator; in automatic control mode, the output of each loop controller is automatically adjusted by the pid software.
Wallet,Suitable for Short Trips,Large Capacity Travel Bag,Dirt-resistant and Easy to Scrub
TAIZHOU ORCHIDLAND IMPORT&EXPORT CO.,LTD , https://www.orchidlandgifts.com