Ultrasonic level gauges and radar level gauges measure differently, which leads to different applications. The radar is based on the dielectric constant of the substance being measured, and the ultrasonic wave is in view of the density of the substance to be tested. Therefore, the measurement effect of the substance radar with a low dielectric constant is compromised, and ultrasonic is generally recommended for solid materials. At the same time, the radar emits electromagnetic waves, which do not require a medium to be transmitted, and the ultrasonic waves are sound waves, which are mechanical waves that require the medium to be transmitted. In addition, the wave has different emission modes. For example, the ultrasonic wave is emitted by the vibration of the piezoelectric material, so it cannot be used in the case of high pressure or negative pressure, and is generally only used in an atmospheric pressure vessel. The radar can be used in high pressure process tanks. Radars have a larger launch angle than ultrasonic waves. Non-contact radars are not recommended for small containers or elongated containers. Guided wave radars are generally recommended. The last is the problem of precision. Of course, the accuracy of the radar is definitely higher than that of the ultrasonic wave. The high-precision radar is definitely used on the storage tank, and the ultrasonic wave is not selected. As for the price, the ultrasonic is generally lower than the radar. Of course, the price of some large-range ultrasonic waves is also very high, such as the range of 6 to 70 meters. At this time, the radar can not reach, and only the ultrasonic wave can be selected!
Ultrasonic level gauge is a series of non-contact, high reliability, low price, maintenance-free level meter, which completely solves the winding, leaking and contact medium brought by pressure transmitter, capacitive and float type measurement methods. Trouble with expensive maintenance, it does not need to contact industrial media to meet the level measurement requirements in most closed/open containers.
Today, with the development of electronic technology, ultrasonic level measuring instruments can measure the range of things from a few centimeters to tens of centimeters, showing extraordinary ability under many harsh conditions.
The inherent principle of ultrasonic level gauge measurement is very simple. The ultrasonic probe is located at the top of the container, and the pulse wave is transmitted to the surface of the measured medium. At the same time, it receives the echo reflected from the surface of the measured object, and the time difference between the transmitted wave and the echo. That is, the round-trip travel time of the sound wave in space to measure the distance of the probe from the surface of the measured medium.
According to the above principle, the main factors affecting the operation of the ultrasonic level gauge are:
First, the impact of speed:
The ultrasonic level gauge has a frequency of 5KHZ-5MHZ in industrial applications and 5HZ-40HZ in the level measurement technology. The formula for calculating the distance from the ultrasonic probe to the medium surface is as follows:
D=t1×C/2
D: the distance from the probe to the surface of the media
T1: the propagation time of the sound wave
C: wave propagation rate
It can be seen that in addition to the measurement accuracy of the propagation time of the acoustic wave, the propagation speed of the acoustic wave plays a decisive role.
The speed of sound changes depending on the medium of communication. In practical applications, a variety of factors affect the media and speed of sound. Today, in order to obtain more accurate measurement results, the ultrasonic level meter can set the sound velocity of different media by degree.
Second, the impact of temperature:
The change in temperature affects the change in sound velocity, and the change in temperature in the normal environment gives a change in sound velocity of 0.17% °C. In actual measurements, a variety of natural factors can cause errors, and advanced measurement systems, including temperature sensors and software functions, can automatically compensate for temperature effects. In practical applications, the temperature of the ultrasonic propagation medium and the temperature of the measured medium are not the same due to the environment around the probe. The measurement system should select an external temperature sensor that is separate from the probe by the built-in temperature sensor combined with the probe according to actual requirements. A more accurate measurement system that places echo reflection references at specific locations from the probe to generate a reference echo to compensate for temperature effects. The effectiveness of this method depends on the accuracy of the placement of the echo reflection reference.
Third, the impact of pressure:
The relationship between temperature changes caused by changes in pressure:
LnT1/T2=1.4LnP1/P2
Although the change in pressure affects the working state of the probe, the change in pressure does not directly result in a change in the speed of sound. Due to the relationship between pressure and temperature: T = KP (K is a constant), the change in pressure affects the change in temperature, which in turn affects the change in sound velocity.
Fourth, the sound wave transmission and transmission:
The inside of the probe has one or more piezoelectric ceramic crystals for the generation and reception of acoustic signals. When the piezoelectric ceramic crystal obtains an electrical signal, it generates a small mechanical vibration to emit sound waves. Similarly, the echo causes the piezoelectric ceramic crystal to generate a small mechanical vibration to emit an electromagnetic signal. The actual method is that a probe plays the dual role of transmitting and receiving.
When the piezoelectric ceramic crystal is excited by electric pulse, it will produce resonance for a period of time. The initial resonance amplitude is very large, and the amplitude will tend to zero as the vibration energy of the probe is weakened. During the resonance period, the resonance covers the echo, making the probe inaccurately determine the echo, which is a few milliseconds, and the corresponding distance range becomes: "blind zone". The relative dead zone of 10mS is 1.7m.
In order to ensure the accuracy of the difference between the transmitted wave and the echo time, the echo signal must have sufficient intensity to generate and convert into an electrical pulse. The strength of the echo signal depends on the strength of the transmitted signal, the characteristics of the propagation medium, the distance traveled and the Measure the characteristics of the medium reflecting surface.
Fifth, the attenuation of strength
The weakening of the intensity during sound wave propagation is due to the absorption of air by the air, which is determined by the viscosity and heat conduction of the air and the behavioral characteristics of the air molecules.
Sixth, the impact of dust
The impact of the dust environment on the speed of sound is very small, but the attenuation of the ultrasonic waves is obvious, which is the main factor hindering the implementation of the ultrasonic scheme. In practical applications, the use of probes with low frequency and special foam surfaces in a dusty environment is very successful.
Seven, the impact of airflow
In an open environment, air acts as a carrier for the ultrasonic waves, and the lateral air flow will cause the propagation path of the sound waves to become longer and longer, and the actual influence is not large.
Eight, the influence of the surface of the measured medium
The echo level ratio of the ultrasonic level gauge depends on the characteristics of the medium to be tested. All the mediums are partially reflected, partially absorbed and partially transmitted to the ultrasonic waves. A dense medium will produce a strong echo, which is the opposite. In the actual measurement, the echo at the liquid interface is much better than the solid. When the echo is generated on the surface of the fixed particle, the angular direction is different, and there is a time difference between each other, which causes the phase to be different and reduces the echo intensity directly reflected back to the probe.
In principle, there are many factors influencing the measurement. Many manufacturers' ultrasonic level meters have software functions such as temperature compensation and echo tracking identification, making the measuring instrument one of the most successful industrial measurement solutions, including liquid level. Solid material level, various warehouse materials, open channel flow, etc., have become the most widely accepted non-contact measurement technology.
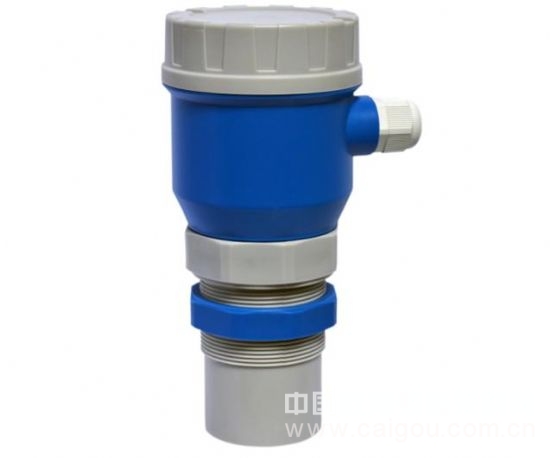
Backpack Mom Bag,Large Capacity Mom Bag,Mom Diaper Bag,Custom Logo Baby Bags
Wuxi Phanpy Baby Products Co., Ltd. , https://www.phanpybreastpump.com